ترکیبات قالبگیری ( ورقهای، تودهای، خمیری، گرانولی) و فرآیند قالبگیری فشاری
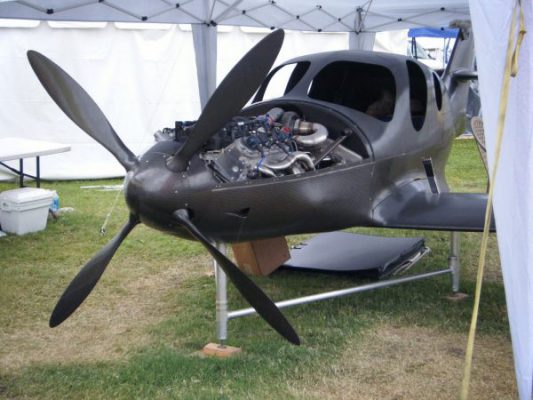
Moulding Compounds (SMC, BMC, DMC, GMC, GMT) and Compression Moulding
عناوین مورد بحث
- آمیزه های قالبگیری و انواع آن
- روش های تهیه آمیزه های ورقه ای
- اجزاء مختلف آمیزه های ورقه ای
- آمیزه های قالبگیری خمیری و توده ای
- آمیزه های قالبگیری گرانولی
- ترکیبات قالبگیری گرمانرم
- قالبگیری فشاری آمیزه های قالبگیری
آمیزه های قالبگیری
بطور کلی آمیزه قالبگیری را میتوان مخلوطی از رزین، مواد پرکننده، الیاف تقویت کننـده، آغازگر، رها سازنده، رنگدانه، پایدار کننده و دیگر مواد افزودنی دانست. این آمیزه هـا معمـولاً بـه شکلی که مناسب برای قالبگیری نهائی است تولید میگردند. بسته به شکل آمیزه فرآیند قـالبگیری میتواند فشاری، ترزیقی و یا انتقالی باشد. کاربرد گسترده این مواد به بهای نسبتاً پائین و امکان بهینه سازی خواص آنها جهت کاربردهای ویژه نسبت داده میشود. آمیزه های قالبگیری بـر پایـه اغلب رزین های گرما سخت وجود دارند که در جدول ۱ به آنها اشاره شده است اما آمیزه های بر پایه رزین پلی استر غیر اشباع سهم عمده را بخود اختصاص میدهند لذا در اینجا تأکید روی آنها بوده است.
در شکل ۱ فلوچارت تولید و ترکیب آمیزه های قالبگیری DMC, BMC, SMC که بر پایه رزین پلـی استر غیر اشباع میباشند نشان داده شده است.
آمیزه قالبگیری ورقه ای (Sheet Moulding Compound, (SMC:
این آمیزه ورقه ای چرم – مانند با ضخامت ۵ – ۳ میلی متر از مواد است که بین دو فـیلم نـازک از پلی اتیلن عرضه می گردد (این فیلم ها قبـل از قـالبگیری آمیـزه برداشـته مـی شـوند) مـاده مـورد استفاده در این آمیزه مخلوطی از الیاف شیشه بریـده شـده و خمیـری از پلـی اسـتر غیـر اشـباع می باشد. یک ترکیب درصد نمونه از این خمیر در جدول ۲ آورده شده اسـت. در ایـن جـدول ۷۰ % وزنی SMC را خمیر تشکیل میدهد و ۳۰ %باقیمانده را الیاف شامل می شود.
تولید SMC با تهیه محلول آبکی (slurry) از مواد در یک دستگاه مخلوط ساز با سرعت بالا آغاز می گردد. همه اجزاء باستثناء تغلیظ کننده بمدت ۱۵ دقیقه با هم مخلوط می شوند. در طی این مدت دمای مخلوط تا حدود ۳۰ درجه سانتی گراد بـالا مـی رود. در ایـن مرحلـه ویسـکوزیته مخلـوط حـدود ۳۰ – Pas 20 می باشد. پس از اینکه عمل مخلوط سازی به اتمـام رسـید مـاده تغلـیظ کننـده (Thickener) اضـافه گردیده و بسرعت طی مدت زمان حدود ۵ دقیقه با بقیه اجـزاء مخلـوط مـی گـردد. در ایـن مرحلـه خمیر آماده است و جهت تلفیق با الیاف به ماشـین SMC منتقـل مـی گـردد. شـماتیک یـک ماشـین SMC در شکل ۲ نشان داده شده است.
دراینجا خمیر تهیه شده با ضخامت معین بـر روی یک فـیلم پلـی اتیلنـی (بـا پهنـای یـک متـر و ضخامت mm 20 – 15) که از رول فیلم بر بستر متحرک دستگاه بـاز مـی شـود ریختـه مـی شـود. سرعت حرکت این فیلم بین ۵ – ۹ m/min می باشد. این فـیلم از زیـر دسـتگاه بـرش الیـاف عبـور می کند و الیاف بلند به طول های mm 25 بریده شده و با سرعتی که درصـد حجمـی مـورد نظـر را فراهم سازد روی فیلم آغشته به خمیر بصورت راندم می نشینند. این فیلم به همـراه فـیلم دیگـر کـه فقظ خمیر روی آن ریخته شده و فاقد الیاف است با هم ساندویچ شده و از یکسری غلطـک عبـور میکنند. این غلطک ها باعث آغشتگی الیاف به رزین، خروج هوا از آمیزه و همچنین تنظیم ضخامت ورق و در نتیجه تنظیم ترکیب درصد الیاف می شود. در انتها ساندویچ تهیه شده بر روی یک غلطک بصورت رول جمع آوری می گردد و در یک فیلم نایلون یا سلوفان پیچیده شده تـا از فرار مونومر جلوگیری شود. این رول سپس به محیط های کنترل از لحاظ دمایی منتقل شـده تـا مرحله تغلیظ شدن در آن سپری شود. در مرحله تغلیظ اجازه داده میشود تا ویسکوزیته ترکیـب به حدی برسد که ورق SMC براحتی قابل جابجایی، برش و قالبگیری باشد.
ویژگی های مواد مورد استفاده در SMC به اختصار ذکرشده اند:
-
الیاف (Fiber):
الیاف شیشه از نوع E معمول ترین نوع الیاف معدنی هستند کـه در تولیـد SMC مـورد استفاده قرار میگیرند. این الیاف می توانند هم بصورت کوتاه و هم بصـورت پیوسـته مـورد استفاده قرار گیرند. اگر خواص ایزوتروپیک از قطعه مد نظـر باشـد الیـاف کوتـاه بـا آرایـش راندم بکار گرفته میشوند و اگر تقویت قطعه در جهتی خاص نیـز مـد نظـر باشـد عـلاوه بـر الیاف کوتاه از الیاف پیوسته تک جهته نیز استفاده می گـردد. آمیـزه هـای SMC را بـر مبنـای شکل الیاف بکار گرفته شده در آنها بصورت زیر طبقه بندی می نمایند:
- SMC – R: آمیزه SMC با آرایش راندم (R) الیاف کوتاه
- SMC – CR: آمیزه SMC دارای آرایش الیاف موازی و پیوسـته (C) و همچنـین آرایـش رانـدم (R) الیاف کوتاه.
- XMC: آمیزه SMC دارای آرایش راندم الیاف کوتاه و آرایش ضربدری (X) الیاف پیوسته.
غالبا درصد وزنی الیاف بصورت یک عدد بعد از حرف مشخصه آرایـش ذکـر مـی شـود. بعنـوان مثال SMC – RC دارای ۳۰ % وزنی از الیاف کوتاه با آرایش اتفـاقی اسـت و SMC – C30R10 دارای ۱۰ % وزنی الیاف کوتاه با آرایش اتفاقی و ۳۰ % وزنی از الیاف پیوسته می باشد. علاوه بر گونه های ذکر شده از SMC ،گونه دیگری موسوم به TMC یا آمیزه قـالبگیری ضـخیم (Thick Moulding Compound) وجود دارد که در فرآیند تولید شبیه به SMC است (شـکل۳) لـیکن ضخامت آن حدود ۵۰mm در مقایسه با ۶mm برای SMC است. این آمیزه برای قالبگیری قطعات ضخیم مناسب است و قالبگیری آن با هر دو فرآیند قالبگیری تزریقی و فشاری امکانپذیر است.
نوع پوشش (sizing) الیاف در خواص مکانیکی SMC و کیفیت قطعه حاصله مؤثر است. الیاف با پوشش سخت در قسمت برش ماشین SMC همبستگی خود را حفظ نموده و در تماس با رزین به سهولت از هم جدا نمی شوند. این امر موجب می گردد تا الیاف بریده شده در حین فرآیند قالبگیری با هم باقی بمانند و این خود منجر به جریان پذیری خـوب آمیـزه SMC در قالـب می گردد اما جفت شدن بین الیاف و رزین بدلیل عدم نفوذ کافی رزین در میان فیلامنت های الیاف ضعیف خواهد بود که این بر روی خواص مکانیکی قطعه اثر خواهد داشت. الیاف با پوشـش نـرم و قابل حل در رزین بهنگام برش در ماشین SMC بـه اجـزاء خـود یعنـی strand هـا و فیلامنـت هـا تقسیم خواهند شد. این امر به توزیع بهتر الیاف در رزین کمک خواهد کرد اما محـدودیت هـایی رادر جریان پذیری رزین بهنگام قالبگیری بدنبال خواهد داشت. محبوس شد هوا در قطعه، نـاقص پـر شدن قالب و موجی شدن سطح قطعه از جمله اثرات آن میباشند.
-
پرکننده ها (Filler):
بطور کلی نقش پرکننده ها در آمیزه های قالبگیری اصلاح خواص رئولوژیکی رزین بگونه ای است که جریان پذیری آن در هنگام قالبگیری مناسب باشد. وجود پرکننـده باعـث بهبـود کیفیت سطح قطعه شده و تغییرات ابعادی (انقباض) قطعه را که ناشی از پخت رزین اسـت کـاهش میدهد. همچنین تأثیر عمده ای در کاهش قیمت تمام شده محصول دارد. در جدول ۳ تعدادی از پرکننده های مهم مورد استفاده در آمیزه های قالبگیری ورقه ای ذکر شده اند.
درصد وزنی پرکننده در آمیزه بستگی به نوع پرکننده، خواص رئولوژیکی رزین و درصـد الیـاف دارد. بطور کلی میزان پرکننده باید در حدی باشد که تر شدگی مناسب سـطح الیـاف بـا رزیـن را مانع نشده و جریان رزین را در قالب دچار اشکال نکند. هر چه درصد الیاف بیشتر باشـد نسـبت پرکننده به رزین کمتر می شود. بطوریکـه نسـبت پرکننـده بـه رزیـن بـرای آمیـزه هـای قـالبگیری ورقه ای با ۳۰%، ۵۰% و ۶۵% الیاف به ترتیب ۱/۵ ،۰/۵ و صفر باشد.
-
آغازگر (Primer):
آغازگر نقش شروع واکنش پخت را به عهـده دارد. بطـور معمـول آغازگرهـای مـورد استفاده در آمیزه های قالبگیری رزین پلـی اسـتر، پراکسـیدهای آلـی بـا فرمـول عمـومی ROOR (تجزیه گشته و این رادیکالها می باشد که در شرایط دمایی خاص به رادیکال های مربوط (RO) با حمله به نواحی غیر اشباع در زنجیره پلیمـری منجـر بـه پخـت رزیـن مـی گردنـد. در جـدول ۴ آغازگرهای مورد استفاده در آمیزه های قالبگیری ورقه ای ذکر شده اند.
معمولترین آنها ترت بوتیل پربنزوات (TBPB) و ۱ و ۱- دی (تـرت بوتیـل پراکسـی) سـیلکوهگزان می باشد که در دمای قالبگیری ۱۴۰ – ۱۶۰ درجه سانتی گراد بگار گرفته می شوند. برای کم کردن زمان قالبگیری و همچنین دمای قالبگیری از پر اکسید های فعال تر مانند t – Butyl Petroctoate استفاده می شود. البته بکارگیری چنین سیستم هایی منجر به کوتاه تر شدن عمر نگهداری ورقه های SMC می شود. بـرای کاهش زمان پخت میتوان از سیستم آغازگر دوتایی نیز استفاده کرد. در این صورت به آغـازگر در دمای بالا درصدی از آغازگر با دمای پایین اضافه می شود.
-
جلوگیری کننده ها (Inhibitors):
در حین تهیه ترکیب قالبگیری و در مدت ذخیره سازی آن امکـان آغـاز تـدریجی واکـنش پخت رزین وجود دارد. نقش جلوگیری کننده ها، ممانعت از شروع واکنش پخـت از آغـاز تهیـه تـا پایان ذخیره سازی ترکیب می باشد. این مواد از خانواده ترکیبات کینـونی مـیباشـد و در مقـادیر بسیار کم (حدود ۰/۰۲%) به فرمولاسیون اضافه میشوند. هیدروکینون و پارا بنزوکینـون از مـواد معمول بدین منظور می باشند. وجود این مواد در فرمولاسیون سرعت پخـت و در نتیجـه افـزایش ویسکوزیته را در مراحل اولیه قالبگیری کاهش می دهد. این امر به بهبود جریان آمیـزه و پرشـدن قالب کمک می کند و لذا از بروز نقایص چون پرنشدن کامل قالب و ایجاد فضـاهای خـالی (Void) در قطعه جلوگیری مینماید.
-
تغلیظ کننده ها (Condenser):
در هنگام قالبگیری ورق SMC می بایـد براحتـی قابـل انتقـال بـه داخـل قالـب و بـرش بـه اندازه های مورد نیاز باشد. نقش تغلیظ کننده افـزایش ویسـکوزیته آمیـزه بـه انـدازه ای اسـت کـه شرایط مورد نظر را فراهم سازد. در واقع عمل تغلـیظ خمیـر رزیـن را از مـایعی بـا ویسـکوزیته حدود ۳۰Pas به ماده ای چرم – مانند با ویسکوزیته در محدوده ۴^۱۰ تا ۵^۱۰ Pas تبدیل می نمایـد. در این شرایط آمیزه غیر چسبنده بوده و قابلیت انعطاف دارد. تغلیظ کننده های معمول برای رزین پلی استر غیر اشباع اکسیدها و هیدرواکسیدهای فلزات گروه IIA مانند CaO, Mg(OH)2) ,Mg) میباشند. عقیده بر این است که افزایش ویسکوزیته رزین بدلیل واکنش یون فلزی با گروه های کربوکسیلیک انتهایی موجود در زنجیره پلیمری و تشکیل زنجیرها و کمپلکس های با جرم ملکولی بالاتر است. نوع، میزان و اندازه ذره تغلیظ کننده و همچنین شرایط رطوبت و دمای نگهداری SMC بر روند افـزایش ویسـکوزیته در طـی فرآینـد تغلـیظ و همچنـین ویسکوزیته نهـایی ترکیـب اثـر دارنـد. در جـدول ۵ اثـر نـوع و میـزان تغلـیظ کننـده بـر افـزایش ویسکوزیته نشان داده شده اند.
در شکل ۴ تغییرات ویسکوزیته خمیر رزین در طی تغلیظ و در هنگام قـالبگیری نشـان داده شـده است.
ویسکوزیته نهایی ورقه SMC در کیفیت قطعه قالبگیری شده نقش بسزایی دارد و باید در محدوده خاصی باشد که بین ۶^۱۰ × ۵۰ و ۶^۱۰ × ۱۳۰ سانتی پواز است. پایین تر از ۶^۱۰ × ۵۰ باعث جدایی رزین از الیاف در طی قالبگیری می شود و بالات از ۶^۱۰ × ۱۳۰ پر شدن ناقص قالب را به دنبال دارد. در طی فرایند قالبگیری ورقه SMC، پیوند های تشکیل شده در عمل تغلیظ بدلیل افزایش حرارت شکسته شده و ویسکوزیته آمیزه کاهش یافته بگونه ای که در قالب جاری می شود و آنـرا پر می کند. بدنبال آن رزین شروع به ژل شـدن نمـوده کـه افـزایش سـریع ویسـکوزیته را شـاهد خواهیم بود. (شکل۴)
ترکیبات قالبگیری DMC, BMC
این ترکیبات بمنظور استفاده از فرآیندهای اتوماتیک تر برای قالبگیری سیستم های رزینـی توسعه یافته اند. این مواد ترکیبات خمیری شکل بوده که به طور ناپیوسته در مخلوط ساز ژاکـت معمول ترین آنها ترت بوتیل پربنزوات (TBPB) و ۱ و ۱- دی (تـرت بوتیـل پراکسـی) سـیلکوهگزان می باشند که در دمای قالبگیری ۱۴۰ – ۱۶۰ درجه سانتی گراد بکار گرفته می شود. برای کم کردن زمان قالبگیری و همچنین دمای قالبگیری از پراکسیدهای فعال تر مانند t – Butyl Peroctoate استفاده می شود. البته بکارگیری چنین سیستم هایی منجر به کوتاه تر شدن عمر نگهداری ورقه های SMC می شود. بـرای کاهش زمان پخت میتوان از سیستم آغازگر دو تایی نیز استفاده کرد. در این صورت به آغـازگر در دمای بالا درصدی از آغازگر با دمای پایین اضافه می شـود. دار بـا تیغـه Z یـا زیگمـا تولیـد می گردند. مخلوط ساز متشکل از دو ظرف یکسان U – شکل از جنس فولاد زد زنگ بـوده کـه درون هر ظرف تیغه ای وجود دارد. این تیغه ها در جهت مخالف هـم چـرخش دارنـد. ظرفیـت ایـن مخلوط سازها بین چند کیلوگرم تا حدود ۱۰ تن می باشد. DMC مخلوطی است از الیاف شیشه بریده شده و خمیری از رزین پلی استر غیـر اشـباع کـه بـا افزودنی های مختلف پر شده است. ترکیب نمونه ای از این خمیر در جدول ۶ آورده شده است.
تولید DMC معمولا در درجه حرارت اتاق انجام می شود هر چند امکان گرم کردن یا سـرد کـردن مخلوط از طریق گردش روغن در ژاکت مخلوط سـاز وجـود دارد. در فرآینـد تولیـد ابتـداء مـواد پودری وزن گردیده و بمدت یک دقیقه با هم مخلوط می شوند. رزین و دیگر مواد افزودنی اضـافه شده و مخلوط سازی بمدت ۳۰ – ۱۵ دقیقه ادامه می یابد. در طی این مدت میتوان مخلـوط سـازی را بمنظور پاک سازی دیواره ظرف متوقف نمود. پس از هموژن شدن مخلوط الیاف تقویت کننده بتدریج اضافه شده و با مخلوط آبکی رزین مخلـوط مـی شـوند. ایـن عمـل حـدود ۵ دقیقـه بطـول می انجامد و هدف آن صرفا توزیع مناسب الیاف در سراسر رزین است. برای مخلوط سازهای با تیغه Z یا زیگما فاصله بین تیغه و دیواره ظرف در محدوده ۳ تا ۱۲ میلی متر است. هـر چـه ایـن فاصله کمتر باشد عمل مخلوط سازی بهتر صورت می گیرد اما احتمال آسیب رسـاندن بـه الیـاف بیشتر میشود.
از آنجایی که الیاف تقویت کننده خواص مکـانیکی (بـویژه مقاومـت ضـربه ای) محصـول نهـایی را تعیین میکنند حفظ طول الیاف در طی عمل مخلـوط سـازی بسـیار اهمیـت دارد. بـدین منظـور از الیاف با تجمع پذیری بالا استفاده می شود. بگونه ای که ماده اتصال دهنده فیلامنت ها به مقدار کم در رزین قابل حل است، لذا در مراحل اولیـه مخلـوط سـازی رزیـن روی تجمـع پـذیری الیـاف تـاثیر چندانی ندارد و الیاف باندازه کافی سخت هستند که مـیتواننـد نیروهـای خمشـی وارده را تحمـل نمایند. بتدریج که ماده نشان دهنده در رزین حل می شود دستجات الیاف به فیلامنت های بـا قطـر کمتر تفکیک شده تا حدی که اجزاء مربوطه تحمل خمشی را نداشته و می شکنند. ایده آل این اسـت که مدت زمان لازم برای مخلوط سازی الیاف برابر با زمانی باشد که طی آن انحلال ماده اتصـال دهنده فیلامنت ها صورت می گیرد. نهایتا ترکیب حاصله در فیلم هایی که مانع از تبخیر مـواد فـرار می شوند بسته بندی گردیده و یا به صورت رشته اکسترود شده و در بشـکه هـای خـاص نگهـداری می شوند.
BMC عموما به ترکیبی اطـلاق مـی گـردد کـه بـر پایـه رزیـن ایزوفتالیـک اسـت و همچنـین عمـل تغلیظ سازی در آن بوسیله MgO صورت می گیرد. عمل تغلیظ سازی میتواند میزان پرکننده را تا ۱۰۰phr تقلیل دهد و لذا امکان افزایش میزان تقویت کننده را فراهم سازد. کـاهش میـزان پرکننـده در BMC ظاهر سطحی بهتری را نسبت به DMC برای آن فراهم می سازد.
ترکیبات قالب گیری گرانولی (GMC)
این ترکیبات بر پایه رزین های گرماسخت مختلف وجود دارند. مزیت عمده ایـن ترکیبـات سـهولت حمل و نقل و همچنین فرآیند پذیری سریع در قالبگیری های تزریقـی و انتقـالی اسـت. تولیـد آنهـا بوسیله آمیزه سازی اجزا مربوطه در اکسترودر صورت می گیرد و معمولا الیـاف کوتـاه بعنـوان تقویت کننده استفاده می گردند. در طی آمیزه سـازی ایـن طـول بـاز کـاهش مـی یابـد ۱mm> لـذا ترکیبات قالبگیری گرانولی خواص مکانیکی نسبتا پایین دارند اما قطعات ساخته شده از آنها ظاهر سطح عالی دارند و این تا حدی به دلیل عدم وجود الگوی الیاف روی سطح قطعه می باشـد. سـاخت ترکیبات قالبگیری گرانولی از رزین پلی استر غیر اشباع غالبا بوسیله تلفیـق یـک پلـی اسـتر غیـر اشباع کریستالین با یک مونـومر غیـر اشـباع کـوپلیمریزه کننـده و دیگـر مـواد افزودنـی و ادامـه آمیزه سازی تا حصول مخلوطی هموژن از اجزا صورت می گیرد.
قالبگیری فشاری آمیزه های قالبگیری
به منظور قالبگیری آمیزه های BMC, DMC, SMC می توان از قالبگیری فشاری استفاده کرد. مراحل کلی فرآیند را می توان بصورت زیر بیان نمود.
مرحله اول:
در این مرحله آمیزه باید باندازه مورد نظـر در قالـب قـرارداده شـود. آمیـزه BMC, DMC را می توان پس از وزن نمودن بصورت توپ گرد درآورد و در وسط قالب قرار داد. آمیزه SMC را میتوان بصورت لایه های مختلف برید و بگونه ای در قالب چید که حدود %۸۰ – ۷۰ سـطح قالب پوشانده شود.
مرحله دوم:
قسمت بالایی قالب (فک متحرک) بسرعت پایین آورده می شود. تا در تماس بـا سـطح مواد قرار گیرد. سپس سرعت کم میشود و به آرامی قالب بطور کامل بسته می شود. سرعت بسته شدن قالب اهمیت دارد، چرا که سرعت بالا منجر به بدام افتادن هوا در قطعه و سرعت پایین منجر به پخت رزین و احتمال پرنشدن قالب میشود.
مرحله سوم:
در این مرحله و پس از بسـته شـدن قالـب بـرای مـدتی قطعـه در قالـب نگـه داشـته میشود تا مراحل پخت رزین باتمام برسد. سـپس قالـب بـاز شـده و قطعـه پخـت شـده بوسـیله میله های خارج کننده به بیرون رانده می شود.
سیکل قالبگیری بستگی به سیستم رزین – آغـازگر، ضـخامت قطعـه و پارامترهـای دیگـر دارد امـا بطور نمونه می توان گفت که در حدود ۴۵ ثانیه به ازای هر میلی متر ضخامت در درجه حرارت بین ۱۲۰ – ۱۶۰ درجه سانتی گراد و فشار بین ۲۰۰ – ۱۰۰۰ psi می باشند.
موارد زیر می توانند در کیفیت قطعه حاصله موثر باشند.
- پیش حرارت دهی مواد قالبگیری
- قالبگیری در محیط خلا
- پوشش دهی درون قالبی
پیش حرارت دهی می تواند زمان قالبگیری کوتاه نموده و پخت یکنواخت تر ترکیب را سبب شود. استفاده از خلاء باعث کاهش تخلخل در قطعه از طریق کاهش حضور هوا شده و در نتیجـه باعث بالا رفتن استحکام قطعه می شود. پوشش دهی درون قالبی که بـه طـرق مختلـف می توانـد انجام شود به منظور بهبود کیفیت سطح قطعه انجام می گیرد. در این روش یک ماده پوشش دهنـده از جنس پلی استر و یا مخلوطی از پلی استر – یورتان در حین پخت به داخل قالب تزریق می گردد که سطح قطعه را کاملا پوشش می دهد. به منظور تزریق لازم است تا قالب بمقدار کـم بـاز شـده و پـــس از تزریـــق مجـــددا بـــرای ادامـــه فرآینـــد پخـــت بســـته می شـــود. همچنـــین می توان مواد پوشش دهنده را بصورت پودر قبل از بستن قالب روی دیواره قالـب پوشـش داد و سپس قالب را بست. درهر حالت پوشش مناسبی از ماده پوشش دهنده روی سـطح قطعـه ایجـاد می گردد.
رفتار جریان
الگوی جریان پذیری آمیزه ورقه ای بسیار حائز اهمیت است و توزیع الیاف، آرایش الیـاف و درجه تخلخل و سایر نقایص موجود در سطح قطعـه تـابعی از آن اسـت. از طـرف دیگـر خـود رفتار جریان آمیزه به عوامل متعددی بستگی دارد که از آن جمله می توان به سرعت بسـته شـدن قالب اشاره نمود. پیشروی لایه های SMC موجود در قالـب و سـرعت پیشـروی آنهـا نسـبت بـه همدیگر تابعی از سرعت بسته شدن قالب است. غالبا در سرعت هـای بـالا و در حـدود ۱۰mm/Sec حرکت لایه های بالایی نسبت به لایه های میانی ثابت است حال آنکه در سرعت هـای کـم و در حـد ۲mm/Sec الگوی جریان تابع ضخامت مواد موجود در قالب است و لایـه هـایی کـه در تمـاس بـا سطح قالب میباشند سریعتر از لایه های میانی حرکت می کننـد. در شـکل ۵ شـماتیک یـک پـرس قالبگیری فشاری نشان داده شده است.
Glass – Mat – Thermoplastic (GMT) Composite
SMC گرمانرم یا کامپوزیت های بر پایه پلیمر های گرمانرم و نمـد الیـاف شیشـه (GMT) از سـال ۱۹۸۰ در صنایع خودرو جهـت سـاخت سـپر و سـایر قسـمت هـای آن اسـتفاده می شـوند. ایـنکامپوزیت ها عموما به صورت ورقه های متراکم بر پایه ماتریس پلی پـروپیلن و الیـاف شیشـه بـا آرایش تک جهته، تصادفی و یا نمدی پیوسته و یا بریده شده طویل می باشند. قبل از فرآیند قالبگیری این ورقه ها در آون (Oven) مادون قرمز تا دمای بالای ذوب ماتریس حـرارت داده می شوند و سپس در حالیکه هنوز داغ می باشند به درون یک قالب فشـاری سـرد منتقـل شـده تـا شکل قطعه نهایی را به خود بگیرند. GMT ماده ساختاری انتخابی عمده در صنایع اتومبیـل شـده است بویژه در جایی که مقاومت ضربه بـالا مـد نظـر اسـت. در مقایسـه بـا فلـزات، GMT نسـبت استحکام به وزن، مقاومت ضربه و مقاومت به مواد شیمیایی و مقاومت به خوردگی بالاتری دارد و همچنین خواص عایقی آن برتر است. در مقایسه با GMT, SMC قابلیت تولید بهتری دارد زیـرا سیکل قالبگیری آن کمتـر اسـت، قابلیـت بازیافـت از طریـق ذوب مجـدد داشـته و عمـر نگهـداری محدودی ندارد. لذا شرایط نگهداری نظیر آنچه در SMC لازم است اینجا وجود نـدارد. عـلاوه بـراین کامپوزیت های GMT گرمانرم داری وزن کمتر و مقاومت ضربه بهتـر می باشـند.
عـلاوه بـر پرکننده های تقویت کننده، الیاف نمدی شیشه به سه شکل زیر میتوانند استفاده شوند:
- نمد با رشته های پیوسته که به صورت تصادفی جهت یافته اند. این نمد در فراهم ساختن سفتی و استحکام در هر سه محور مفید است.
- نمد با الیاف بلند تک جهته، این آرایش سفتی و استحکام در جهت الیاف فراهم می سازد.
- نمد با الیاف بریده شده طویل که از لحاظ سهولت جاری شدن ترکیب در فرآینـد قـالبگیری بـه لحاظ مصرف انرژی کمک کرده ضمن اینکه مینیمم کاهش در سفتی را ایجاد می نمایند.
لحاظ مصرف انرژی کمک کرده ضمن اینکه مینیمم کاهش در سفتی را ایجاد می نمایند. استفاده از پرکننده های معدنی در GMT هم بمنظور بهبود کارآیی و هم جهت کاهش قیمـت تمـام شده می باشد. این پرکننده ها ضریب انبساط حرارتی کمتری نسبت به ماتریس پلی پروپیلن دارنـد لذا قطعه قالبگیری شده دارای انقباض کمتر و معایب سطح کمتر خواهد بـود. بـدلیل بـالاتر بـودن ضریب هدایت حرارتی این پرکننده ها نسبت به ماتریس پلی پروپیلن ذوب و توزیع حرارت سریعتر بوده و این منجر به بهتر شدن کیفیت ذوب و مشکلات کمتر بواسطه انقباض دیفرانسیلی و پیچش خواهد بود. بالاتر بودن ضریب هدایت حرارتی در هنگام سرد شدن قطعه منجر به کوتاه تـر شـدن سیکل قالبگیری می شود. همه این موارد باعث رقابتی شدن GMT در مقابل SMC می شوند.
مقایسه GMT و SMC با استیل در استفاده از آنها در صنایع خودرو
از جمله مزایای ایم مواد نسبت به استیل عبارتند از:
- وزن کمتر
- مقاومت به خوردگی عالی
- تجهیزات ساخت ارزانتر
- کوتاه تر بودن فرایند ساخت از نظر تجهیزاتی
- مقاومت بهتر به ضربه های جزیی
فرایند ساخت
در شمای زیر فرآیند ساخت GMT نشان داده شده است. این فرآیند بصورت لایه گذاری پیوسـته می باشد.
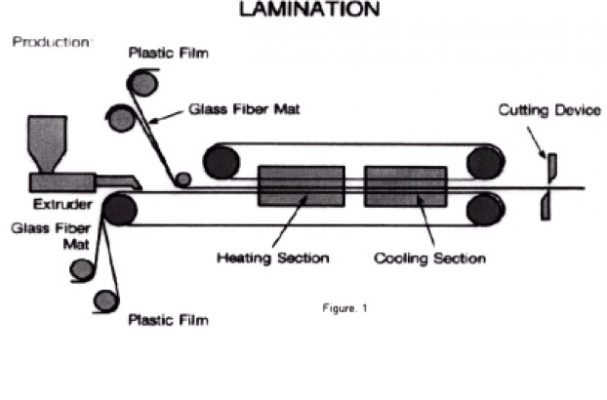
نمونه فرمولاسیون GMT و مقایسه خواص آن با SMC استاندارد
سوالات متداول
آمیزه های قالبگیری چیست؟
طور کلی آمیزه قالبگیری را میتوان مخلوطی از رزین، مواد پرکننده، الیاف تقویت کننـده، آغازگر، رها سازنده، رنگدانه، پایدار کننده و دیگر مواد افزودنی دانست.
آمیزه قالبگیری ورقه ای چیست؟
این آمیزه ورقه ای چرم – مانند با ضخامت ۵ – ۳ میلی متر از مواد است که بین دو فـیلم نـازک از پلی اتیلن عرضه می گردد
از کدام نوع الیاف شیشه در تولید SMC استفاده می گردد؟
الیاف شیشه از نوع E معمول ترین نوع الیاف معدنی هستند کـه در تولیـد SMC مـورد استفاده قرار میگیرند. این الیاف می توانند هم بصورت کوتاه و هم بصـورت پیوسـته مـورد استفاده قرار گیرند.
نقش پرکننده ها در آمیزه های قالبگیری چیست؟
بطور کلی نقش پرکننده ها در آمیزه های قالبگیری اصلاح خواص رئولوژیکی رزین بگونه ای است که جریان پذیری آن در هنگام قالبگیری مناسب باشد.
بسیار عالی بود استفاده کردم از محتویات خوبتون موفق باشید
با سلام امکان دارد که لیست References مطالب بالا ارائه گردد. با تشکر